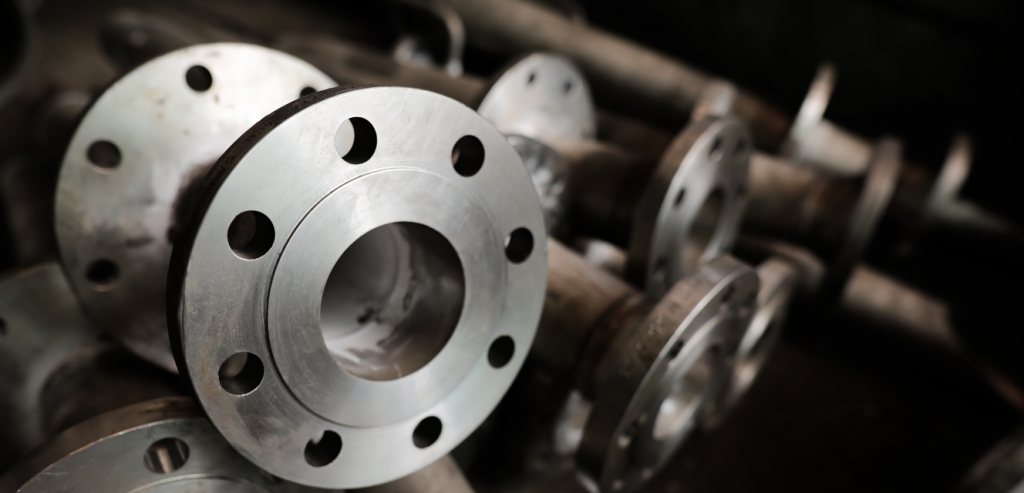
Linear-Elastic Stress Analysis
This is a static analysis that considers only the linear portion of the material stress-strain curve. Basic benefits include speed of solution and ability to use a high mesh refinement, and/or high mid-node counts. Main negatives include being limited to stresses below the proportional limit of the curve, and requiring stress linearization in the design process. Limiting design stress intensities (Pm, Pm+Pb, Pm+Pb+Q) are not always at the highest stress shown on the model and requires diligent examination of the model. Examples of SMPES, LLC’s work using Linear-Elastic Stress Analysis.
The mesh is hand created. That is, each line is created manually by either direct entry or copy and pasting. Algor, in their results tab, for plate elements, has a direct evaluation of membrane stress intensity (Pm) and membrane plus bending stress intensity (Pm+Pb), which are used against ASME Code allowables. The maximum tresca stress intensity value found using the probe search in Algor is used to evaluate for fatigue. The Algor maximum value tag could also be used to identify this highest stress intensity value.
A different mobile tank was analyzed for structural strength of the floor and reinforcement beams. Again, the mesh was entirely hand made and maximum stress intensities were evaluated against Pm and Pm+Pb Code criteria. Loading was only applied to the floor in this analysis.
Stress Linearization
In order to evaluate stress intensities for design purposes, linear elastic stresses require stress linearization. ASME VIII Div. 2 Code requires the average membrane stress intensities across a cross-section to be less than a specified value (Sm). Also, the Code limits membrane plus bending (Pm+Pb) across a cross-section to be less than a specified value (1.5Sm). In order to obtain these average stress intensities across the cross section, stress linearization is employed. This process unfortunately requires due diligence and patience as the maximum Pm and Pm+Pb are not necessarily at the highest stress intensity on the model. Two nodes on opposite sides of a cross-section are selected. Algor has an automatic stress linearization feature that allows calculation of Pm and Pm+Pb from direct entry of these two nodes.
A heat exchanger is evaulated for maixmum stress intensities in the shell adjacent to the tubesheet-to-shell juncture. Various nodal cross section points are investigated. The above image shows the location and the seven data points used to calculate the linearized stress intensities. Typically, at a minimum, three elements across the cross-section are required to properly capture bending stresses; however, mid-nodes are used instead for this purpose.
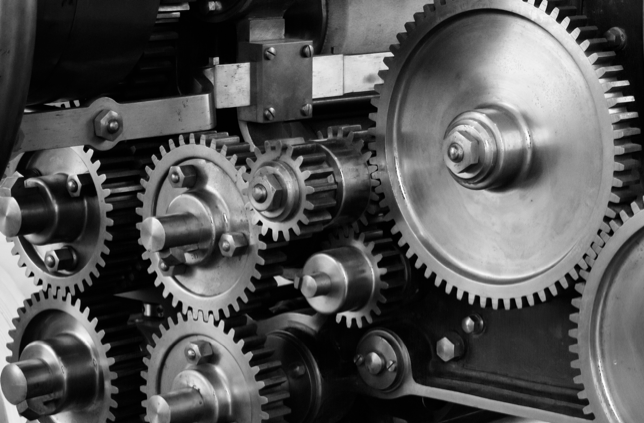
Non-Linear Stress Analysis-Plastic Collapse With Mechanical Event Simulation
Accounting for material non-linearality means accounting for the material stress-strain curve properties outside of a purely linear elastic range. There are different ways of accounting for this non-linearality. Either a straight line hardening coeffient can be used to approximate the material hardening effect, or curve data can be used to provide a truer means of matching the actual stress-strain curve profile. A hardening coefficient essentially creates two straight lines to represent the material curve, one for the linear elastic portion and the other to represent the non-linear portion of the curve. Curve data is based on a set up data points of stress versus strain, which will eventually create a multitude of straight line between these data points. Thus, the more data sets, the more representative it will be of the real curve. Next, in the non-linear analysis, the FE analysis can consider geometry changes, which is where much of the added time in a non-linear analysis comes from because a stiffness matrix is recalculated at each step. A step is dependent upon user data input as to how often this matrix should be recalculated. With non-linear analysis, there is also consideration for small and large displacements. For example, a long plastic object will have large displacements. Thus, large displacement theory is necessary to get proper results. Mechanical Event Simulation (MES) allows for actual motion which can lead to impact, inertial effects, and more realistic surface-to-surface effects.
Resources for Materials, Welding, and NDE
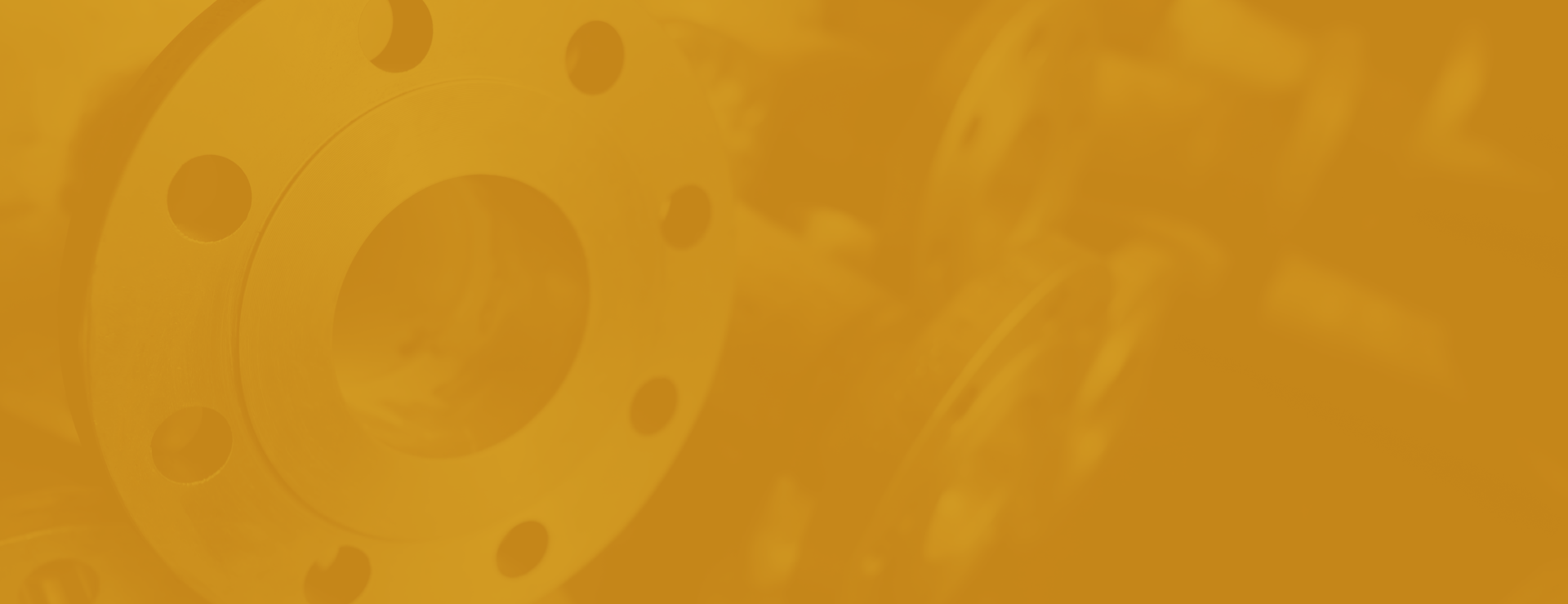
Are You Running At Optimal Conditions?
Saba can run a Failure Analysis to determine what went wrong, make the correct repairs, and determine whether components are Fit for Service.