FEA Engineering Modeling and Welding Techniques for Lasting Equipment Integrity
When addressing repeated plant issues, a first step is to reproduce it, in this case using finite element analysis (FEA) modeling. The loading on this nozzle with repeated cracking is primarily due to the load placed on it by its connecting piping. To make matters worse, this line is refractory lined, and as thermal expansion/contraction ensues, the refractory becomes damages and the high heat exposure to both the nozzle and shell create metallurgical issues. With multiple closely-spaced vessel having interconnecting piping with high thermal growth, it was necessary to model the unit, inclusive to the reactor and its rigid internal bed structure, a heat exchanger and storage tank. As expansion joints and spring support are important to the overall structural rigidity/flexibility, these items were also included. The FEA model indicated moderate stress levels on this nozzle. However, over the years of localized overheating, the metal became spheriodized and graphitized at various locations around the nozzle. A repair would require post-weld heat treatment (PWHT) for this 1-1/4 Cr, ½ Mo plate material. However, performing a PWHT on this old-aged equipment is not wise. Thus, a temper bead technique was proposed.
Unfortunately, this welding technique can be easily performed incorrectly and produce unacceptable weld and heat affected zone hardness. A procedure was provided to the plant AND personnel from SMPES, LLC worked with both the maintenance foreman and the welder to produce a practice run for the main repair. This practice run was taking a sample out of the shell near the nozzle. One, this allowed laboratory testing of the old plate, and two, this allowed confirmation of a properly executed temper bead repair. Lab analysis indicated that some areas with spheroidization had lost 1/3 rd of its strength, while other areas had high hardness graphitization. The new welds had acceptable hardness levels.
The trick with this repair was placing the new weld metal in areas away from the graphitization. Field testing was performed to plot out these areas and then a new nozzle design was created, using an insert design with partial plug welds. Further, using the FEA model, the connecting piping was revised to allow for a more flexible expansion joint. The new nozzle and connecting piping now showed much improved stress and deflection levels. Without this repair, there was the potential of condemning this highly costly sulfuric acid reactor. Instead, a suitable repair was made. As of this writing, this repair has worked as planned for over five years with no further repairs necessary to this nozzle.
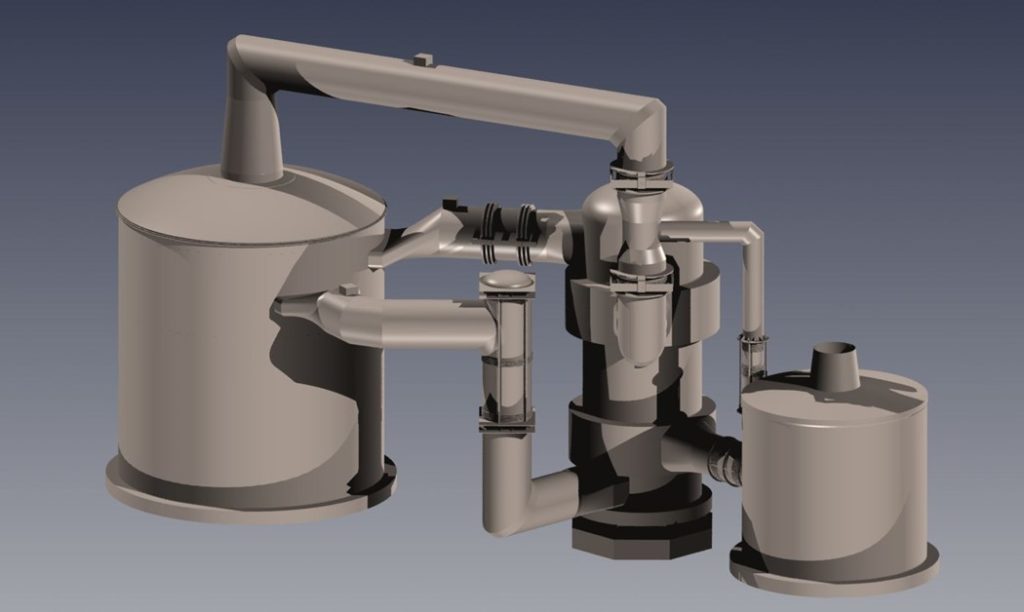