Evaluating Fitness-for-Service of a Damaged Heat Exchanger
It’s never desirable to have a new piece of equipment show up at the site damaged. In many cases, this would be a warranty repair and the damage component replaced. However, under certain circumstances, due to startup deadlines, it may be more desirable to have this damaged equipment evaluated for fitness-for-service. One such incident occurred when a new high temperature heat exchanger hit a bridge during delivery.
On top of that it hit one of the most critical equipment components, the half bellow thick expansion joint. Using provided 3D scan data, the impact size and depth, and resultantly the accrued plastic strain, were recreated using the explicit solver in the Abaqus FEA program. Prior to creating this impact damage, the forming strains of the EJ were established again using the explicit solver. These stresses/strains were carried over to a cyclic-creep cyclic-by-cycle analysis model by use of an initial state function. This CBC cyclic-creep analysis was evaluated first for the undamaged model and then for the damage model. Strain-rate hardening data was obtained for the austenitic stainless steel EJ and used in the FEA model. Loading was applied in the model through several cycles, which included a long-term creep step in each cycle. Total cyclic strains were determined, with inclusion to elastic, plastic, and creep relaxation strains. Also, long-term creep strains were determined. ASME Nuclear Code III.5 was used for the cyclic-creep calculations. It was determined that after a few cycles the strains in the dent reached elastic shakedown and that the cyclic-creep life met the original design criteria. Potential damage to the welds was included in this analysis, using FE-Safe/Verity.
Final recommendations were made to make surface and volumetric examinations of the welds in the vicinity of the impact damage. As of this writing, the equipment has been in service for 5-yrs with no reported issues.
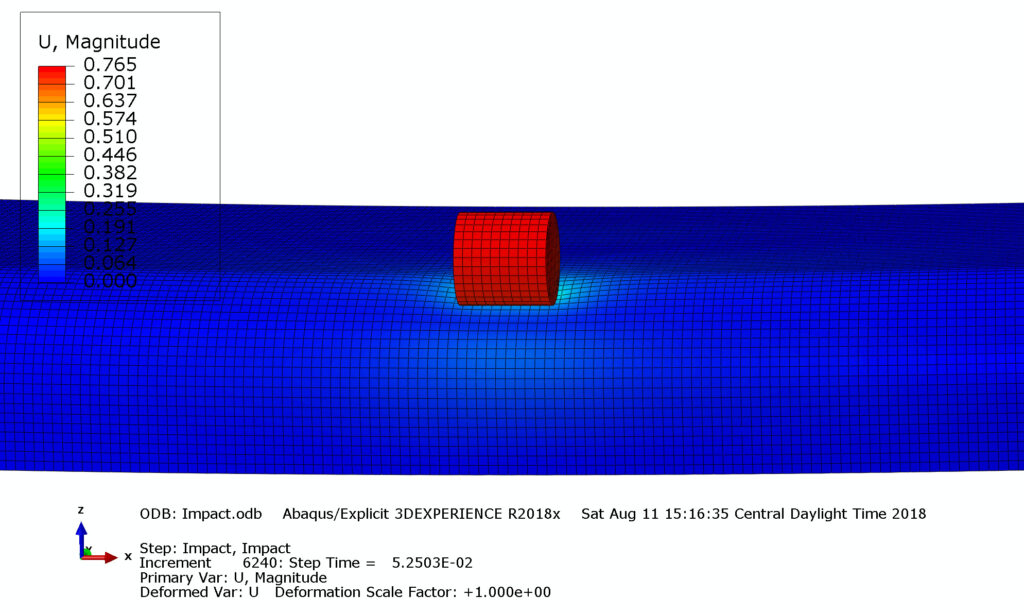