Optimizing Performance with Detailed Thermal and Structural Analysis
Detailed 3D CFD and FEA models were created of the redesign of an air grid in a fluidized bed, including about 2000 grid openings and the same number of nozzles. A transient Eulerian fluid with Lagrangian particle computational fluid dynamics (CFD) study of various stages of operation were conducted. All solid metal and refractory components were included in the model. Particles were supplied to the fluidized bed space via an injector nozzle. These particles heated up due to the burning process and then radiated heat back to the grid.
The transient temperatures were then mapped to an equivalent 3D finite element analysis model, where static and thermal/pressure fatigue was evaluated. Non-creep regime studies were conducted per the non-linear methods of ASME Section VIII Div. 2 for non-fillet weld items. Weld fatigue per the Equivalent Structural Stress (ESS) method, using the Verity program, was used to evaluate those fillet weld items, as well as butt-joint welds of non-smooth contour. Cyclic-creep was evaluated per Nuclear Code ASME Section III.5. Numerous sub-models were created to evaluate various fatigue source locations.
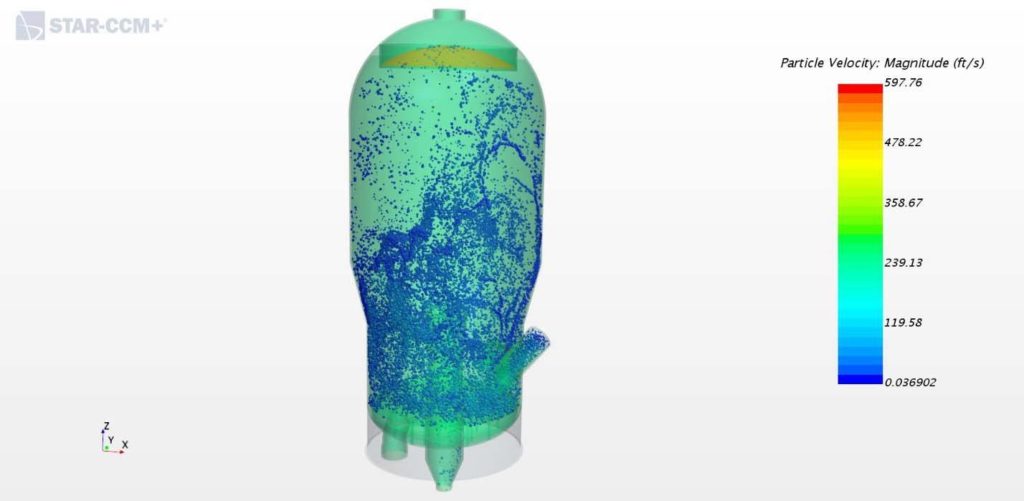