Effective Engineering Repair Solutions for Corrosion Damage
Clearly it is highly undesirable to have your equipment fail not long after startup. But, we at SMPES, LLC are here to quickly help determine the cause and then proceed to how to get your unit back up and running as quickly and safely as possible. The study here is of a new chemical reactor/heat exchanger that experienced through-wall cracking at a body flange weld quite shortly after initial operation. A field inspection was made, and directions were provided for extracting boat samples for metallurgical failure analysis. SMPES, LLC conducted the metallurgical failure analysis with the assistance of our 3 rd party lab.
A high hardness was observed at the dissimilar metal weld joint. This aggravated the clear development of a wet corrosive media that produced stress-assisted corrosion cracking. Of interest was that the crack, although starting at the weld root in a zone of high hardness did not continue alone the HAZ high hardness zone. An FEA study showed that the path of high stresses proceeding radially outward from the vessel did not follow this weld line. This study was then repeated using Abaqus XFEM fracture mechanics solver which was able to reproduce the exact crack path. With the source of the failure known, the next step was to devise a repair plan; due to long lead times, a body flange placement at this time was not a viable option. Thus, the cracks were ground out and a weld repair made, now with an advised modified welding procedure to reduce the weld’s HAZ high hardness.
Being a corrosion related cracking source, the likelihood that micro-cracks would be left in the metal existed. As a result, a traditional fracture mechanics study using FEA was performed. Delta KI and JI plots were created along a predicted crack path. Corrosion cracking non-linear growth rates were calculated using ASM handbook resource. Using this data, a life expectancy was calculated and, resultantly, the equipment was allowed to operate until several months later when the body flange replacement was performed. The equipment operated safely during this time and the new body flanges are now installed. This project highlights the benefits SMPES, LLC offers, with one engineer with the knowledge of metallurgy, corrosion, welding, FEA, and fracture mechanics, can take a difficult situation and quickly find a suitable resolution.
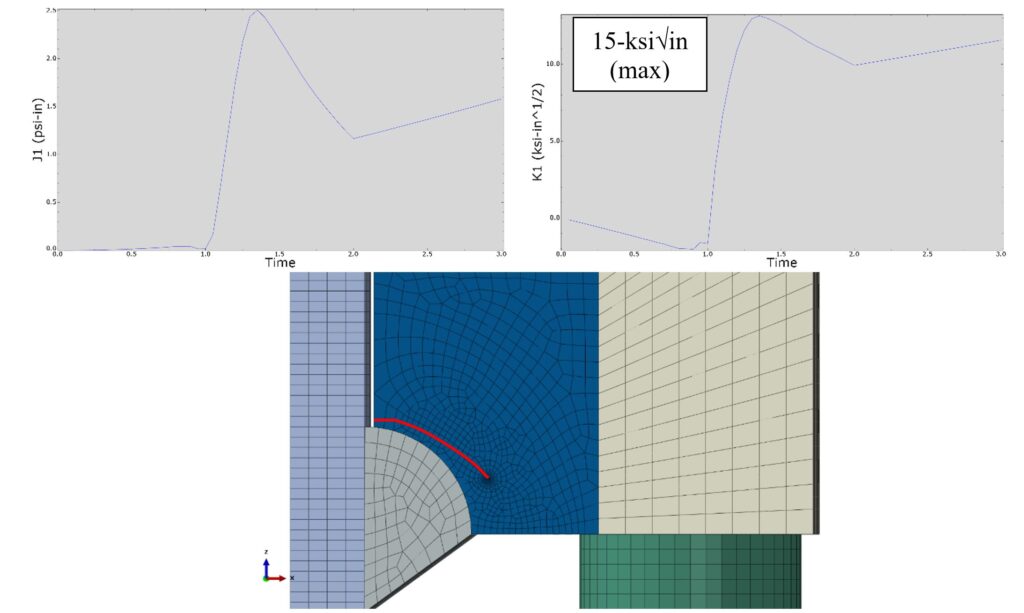